Improving The Manufacturing Process Through The Use of An Energy Savings Performance Contract (ESPC)
By: Kristen Wrona
PINPOINTING INEFFICIENCY
Efficiency in manufacturing is more than simple input and output numbers (i.e., productivity). It also encompasses reducing waste and rework, improving quality, eliminating unscheduled downtime, and enhancing worker safety. As a result, setting production efficiency goals expands the focus beyond just productivity. These goals now include:
- Produce high-quality products
- Provide a safe work environment
- Improve overall equipment effectiveness
- Reduce changeover times
- Minimize downtime
- Reduce energy consumption
- Lower operational costs
- Slash scrap rates
- Streamline processes
- Optimize inventory
- Upgrade legacy machines/equipment
Efficiency in the manufacturing process enables companies to meet and even exceed their production goals. But how can these efficiencies be achieved when capital is limited? The answer lies in implementing an energy efficiency project that pays for itself.
WHY IS EFFICIENCY IN MANUFACTURING IMPORTANT
Efficiency is important because it:
- Improves quality: Efficiency results in higher production rates and faster lead times. With more time available for quality control measures and thorough inspections, it becomes easier to maintain and enhance product quality.
- Reduces costs: With an efficient manufacturing process, less labor, materials, and energy are required lowering expenses.
- Boosts profits: An efficient and sustainable manufacturing process will produce more products with the same resources, thus increasing profits.
- Increases employee safety: An optimized process reduces the likelihood of accidents, ensuring a safer working environment.
DETERMINING WHERE EFFICIENCY IMPROVEMENTS CAN BE MADE
Auditing your manufacturing process will identify where improvements can be made to bring about efficiency, as illustrated in the graphic below.
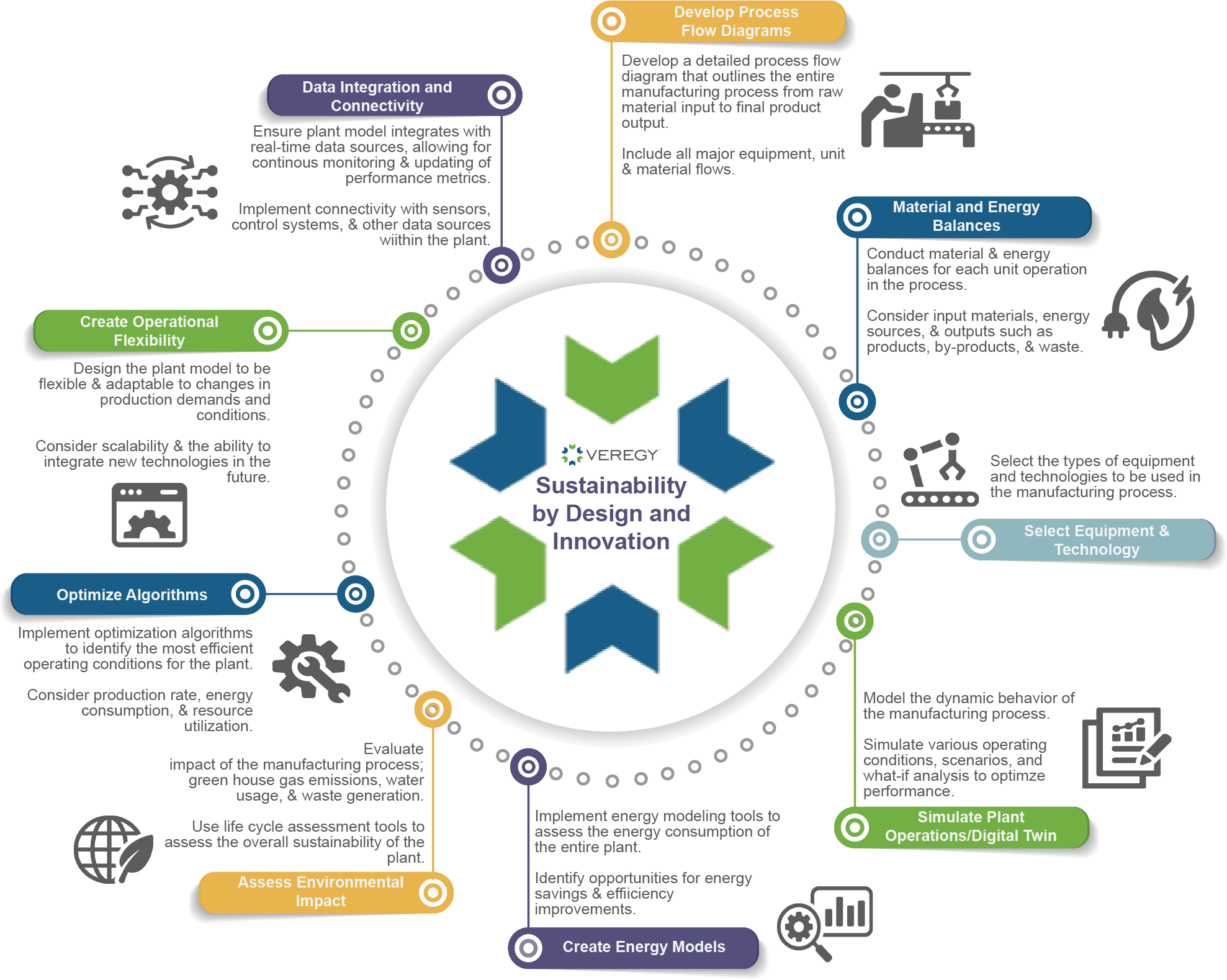
- Optimize Algorithms/Identify Bottlenecks: Typically, these appear on the production line and shop floor. This could include outdated equipment, material and personnel movement on the manufacturing floor, single point-of-failure (e.g., air-compressor systems), labor labor-intensive activities-vs-automation. Conducting a bottleneck analysis leads to pinpointing areas where efficiencies can take place and systems can be optimized. This can be completed using Envision by Veregy or other bottleneck analysis.
- Reduce Waste/Simulate Plant Operations/Digital Twin: Obvious waste areas include recycling, rework, or scrap as a result of the manufacturing process. However, waste can consist of items like workstation setup and product travel time across the manufacturing floor. By creating a digital twin of the manufacturing floor and processes, an evaluation can be made. Simulate and analyze “what if scenarios” before making physical changes. 1 2
- Create Operational Flexibility/Implement Lean Practices: Lean practices include the 5S system eliminates clutter, minimizes search times, and standardizes processes; Kaizen Events provides continuous improvements; and Value-Stream Mapping helps visualize the entire production process 3 4 5
- Develop Process Flow Diagrams/Establish Standard Work Practice: By developing standard work processes or sequence-of-operation, consistency and quality are maintained, thus eliminating rework and reducing waste.
- Maintain Good Housekeeping: Housekeeping includes keeping work areas clean, which minimizes contamination across production lines as well as equipment. It also ensures materials and tools are kept in a consistent location, reducing time wasted while employees seek out needed equipment/materials.
- Material and Energy Balances/Audit Existing Processes: As technology advances and waste is reduced, evaluating the existing processes is still required to determine whether steps can be removed, revised, or combined, all of which lead to efficiencies.
- Train Employees Regularly: This training includes initial training, as well as performance (equipment metrics to ensure the equipment is performing according to the manufacturer’s specifications), operational (protocols for equipment and manufacturer’s specifications), and remedial training.
- Develop Predictive and Preventative Maintenance: By minimizing unscheduled maintenance, production downtimes are eliminated. Furthermore, maintenance and equipment replacement can be performed during scheduled production outages.
- Select Equipment and Technologies/Automate: Automation is more than robotics. Automation can replace manual, time-consuming, and error-prone tasks (such as data collection) that provide real-time relevance.
- Data Integration/Use Real-Time Data: The use of real-time data allows for equipment adjustments if it is out of calibration, thus reducing waste, lending to predictive maintenance needs, and producing consistent quality end products.
TYPES OF IMPROVEMENTS AND HOW THEY TIE TO ECMS/FIMS AND IMPLEMENTATION WITHIN AN ENERGY SAVINGS PROJECT
In order to improve manufacturing efficiency without upfront capital, each improvement to eliminate bottlenecks, reduce waste, automate, and provide predictive and preventative maintenance must produce a calculable energy savings that, together with operations, maintenance, repair, and replacement (OMRR) will pay for itself. Energy Conservation Measures (ECMs) and/or Facility Improvement Measures(FIMs) examples include:
- EMCS (Energy Management Control System): Adding controls/points to existing and new equipment and remote monitoring (e.g. Orchestrate)
Benefits: Tracks equipment calibration, resulting in less rework/waste, optimizes the equipment uptime, and allows for predictive maintenance. - HVAC: Infrared heaters to replace traditional HVAC on the manufacturing floor.
Benefits: Reduced energy consumption, improved worker comfort and safety, increased uptime. - Lighting Upgrades and Controls: Upgrading to LED fixtures throughout the manufacturing floor.
Benefits: Reduced energy consumption, increased uptime, improved light levels and color rendering, consistency of stock reducing maintenance costs, and predictive maintenance. - Water and Wastewater Systems: Separate sanitary water and industrial wastewater systems.
Benefits: Reduces unnecessary amounts of water running through industrial wastewater systems and higher costs of treatment. - Process Improvements/Oven/Autoclave Controls
Benefits: Minimizes reprocessing of parts and waste, saves energy, extends the life of the heating elements, and standardizes work practices. - Process Improvements/Decentralize and Right-Sized Air Compressor Systems
Benefits: Increases system redundancy, eliminates single-point-of-failure, increases uptime, provides consistent air work spaces, matches instantaneous production of compressed air with near real-time manufacturing requirements.
CONCLUSION
Without a comprehensive understanding of the full manufacturing process and clear identification of performance gaps, true optimization and efficiency improvements aren’t possible. Taking a holistic approach to manufacturing efficiency can help avoid costly capital expenditures on one-off equipment failures. Veregy’s expertise enables a thorough audit to pinpoint where and what parts of the process should be upgraded to maximize return on investment.
Additionally, by leveraging performance contracting, manufacturers can improve process efficiency, reduce unscheduled downtime, extend equipment life, and minimize—or even eliminate—upfront capital expenditures. Partnering with Veregy leads to greater efficiency, increased output, and reduced energy use—a win-win-win.
Endnotes
Sources
- https://www.teamsense.com/blog/improving-manufacturing-efficiency
- https://www.machinemetrics.com/blog/production-efficiency
- https://www.machinemetrics.com/blog/manufacturing-efficiency
- https://www.sustainablemanufacturingexpo.com/en/articles/improve-factory-efficiency-guide.html
- https://safetyculture.com/topics/manufacturing-operations/manufacturing-efficiency/